The Purpose of PPE for Construction Workers
Written by Staff Writer
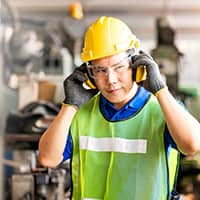
Falling objects, sharp edges, chemicals and many other potentially dangerous conditions exist on any jobsite. The Occupational Safety and Health Administration (OSHA) maintains construction industry regulations for employers and employees to help minimize the risks of such hazards. These include standards for the use of personal protective equipment (PPE).
Personal protective equipment used in construction sites includes items designed to protect your whole body — including your head, eyes, face, lungs, hands and more.
Here, we will cover some of the most common PPE you will encounter while working in construction and explore some of the ways you can educate yourself about those requirements to protect yourself and your fellow employees.
Types of Personal Protective Equipment Used in Construction
OSHA’s guidelines cover all types of construction PPE used to protect against hazards on a jobsite. These types of PPE include:
Occupational Foot Protection
Many worksites require workers to wear steel-toed work boots or similar hard-toed shoes. Regulators have outlined guidelines for the role footwear should perform in preventing specific working hazards. For example, different shoes and boots can provide chemical resistance, puncture resistance and slip resistance.
Head Protection
Regulators require employees working in areas where there is a possible risk of head injury to wear head protection. Falling objects are an obvious risk, but burns, electrical shock and other hazards can also cause head injuries.
Hard hats are the type of head protection most people are familiar with. Regulators classify two types of head protection for impact and three classes of head protection for electrical risks.
Type I head coverings protect from blows to the top of the head. Type II head coverings protect from blows to the top and sides of the head. Electrical classifications include Class G for low voltage risks, Class E for high voltage risks and Class C for conductive risks.
Hearing Protection
Sometimes worksites are loud enough to damage your hearing, such as when the work requires heavy equipment. Even when a single source of sound is not damaging, noise repeated or amplified over a long period can still cause damage.
Regulations require employers to provide hearing protection whenever noise levels exceed 85 dBA. The protective devices can include earplugs, earmuffs or other types of sound-dampening equipment.
Eye and Face Protection
The list of potential eye and face hazards is extensive, including “flying particles, molten metal, liquid chemicals, acids or caustic liquids, chemical gases or vapors, or potentially injurious light radiation.” With so many potential risks, the importance of PPE is obvious.
Glasses, goggles and face shields are the most common types of eye and face coverings in the workplace. Which type you use will depend on the risks involved. For example, glasses might be fine for framing a building but do not provide sufficient protection for welding.
Respiratory Protection
Worksites can present numerous potential respiratory risks to contractors. According to regulators, these can include “harmful dusts, fogs, fumes, mists, gases, smokes, sprays, or vapors.” To protect your lungs and respiratory system, it’s important to wear appropriate gear — like a respirator.
Manufacturers make many different types of respirators to protect against specific dangers. It is not a one-size-fits-all type of equipment, which is why employers must identify the specific risks and provide you with the appropriate respirator for the situation, including verifying fit and correct filtration.
Personal Fall Arrest Systems (PFAS)
A personal fall arrest system stops an employee safely in the event of a fall from a working level. If you are exposed to fall hazards, it’s extremely important to wear appropriate PFAS gear which can include belts, lifelines and lanyards.
Which you use will depend on the circumstances. Extensive specifications dictate situations where each device is appropriate. As with other types of personal protective equipment, employers must identify the need for and provide PFAS devices to employees.
For example, according to regulators, “Lifelines shall be secured above the point of operation to an anchorage or structural member capable of supporting a minimum dead weight of 5,400 pounds.”
Employers should explain that PFAS devices are only supposed to be used once. If they are used repeatedly, they could fail. That’s why employers must ensure that used devices are removed from service until they can be inspected and reviewed.
Who Needs to Provide PPE?
The primary responsibility for safety equipment rests on the shoulders of the employer. There are many reasons for this, including the fact that a single worker can’t know every risk they will face, especially if they are new to the job.
Employers must identify all risks and attempt to address them using engineering, work practices and administrative controls first.
For example, an employer could build a barrier between a hazard and employees as an engineering control. Or they could change the way employees work to avoid the hazard as a work practice solution. Only once these types of solutions are exhausted should employers turn to protective gear.
When the employer determines what PPE is necessary, they must select the right gear, provide suitable devices and train employees on the use and care of each item. Management also needs to maintain the gear and replace it once it’s worn or damaged. In almost all cases, the employer is responsible for paying for this equipment. Employers cannot force employees to pay for PPE as a cost-saving measure.
Workplace Safety Training
Educating yourself on construction site hazards and construction safety is well worth your time.
At OSHA Education Center, we offer fully online courses designed to help you understand the ins and outs of workplace hazards, regulatory requirements, PPE and more.
10-Hour OSHA Training for Construction is a general safety awareness program that covers regulations and requirements for construction workplace safety. This is a recommended general workplace safety training for workers.
This course is perfect for entry-level workers in construction, demolition, building development and other similar industries. OSHA Outreach Training is optional and voluntary. Some employers, unions, states and other jurisdictions require you to complete this type of course. Even if it isn’t required, the information in the course can help you protect yourself and others on the jobsite.
Once you complete the course, you will earn an official OSHA 10 card from the U.S. Department of Labor (DOL).
OSHA 10 and OSHA 30 — which we also offer — are part of the OSHA Outreach Training Program. The program is a partnership with the DOL to promote workplace safety. We are an OSHA-authorized provider of Outreach Training.
For even more information, our one-hour OSHA Personal Protective Equipment Certificate course teaches you general requirements for personal protective equipment, helps you learn to assess hazards and familiarizes you with different types of protective equipment.
Reasons to Choose OSHA Education Center
As a trusted provider of workplace safety and compliance training, we offer students significant value for their money. Our courses are convenient, high-quality programs available from any internet-connected device. Some of these benefits include:
- Working from anywhere at your own pace
- Starting and stopping the course as many times as you need
- Automatic progress saving
- Email access to a course trainer
- Free delivery of your official OSHA card
We understand that your time is valuable, which is why we make our courses as user-friendly as possible. Our goal is to help you get the education you need without the hassle of in-person classes. You also have up to 180 days to complete your course — approximately six months. You have plenty of time to reach your goal. Sign up and start learning today!